Automotive Customer Case Study
Previous Situation
Previously all PPE items were held in a central store. The store was manned by 3 people. The store was on average a 5 minute (there and back) walk from the operator’s place of work. Operators went to a hatch in the stores and requested the items. The stores man noted the items that were taken, the user, and the quantity. The store was manned from 7am to 5pm, even though the factory run 24 hours a day.
Reporting was collated by the storeman from the issuances from the store. This was passed to the Purchasing Manager on a monthly basis.
Main issues
• Excessively high glove usage as there was no restriction on either the type or quantity of the item
• Stores have been left open at night and excessive stock been taken and not booked out. This included items that were not PPE.
• Stores man spending most of there time issuing stock rather than focussing on value-added tasks
• Large walk around times of operators
• Stock not been available 24 x 7
Present Situation
Automotive customer installed 2 x IVendm solutions one in each building. PPE is now available 24 hours a day 7 days a week. Walk around time is greatly reduced as operators now walk to an iVend solution close to their place of work. All PPE issuances from the store have been eliminated as these are issued from the IVendm.
All item issuances are automatically recorded by the user, item, quantity and time and date stamped and no paperwork is required from stores. All information is now real-time from Sourcerer rather than monthly reporting.
Restocking is based on information from internet reports available from Sourcerer and the need to cycle count stock before placing orders has been eliminated.
The customer has also used this opportunity to introduce laundered gloves into IVendm. Operators were reluctant to accept these from the storeman as users would insist on new gloves. However now operators can only be issued items from IVendm, which takes away any potential confrontation with the storeman.
Hard Cost Savings
This customer realised a 34% reduction in PPE in year 1. The Purchasing Manager used the real-time information to monitor usage and users showing anomalous usage were asked to report for “counselling sessions” to explain and correct user behaviour. Hard cost savings are due to:
Reduced pilferage
§ Real-time data identified users that were taking items not required for their job.
– 24 x 7 access to PPE meant that nobody required access to the stores out of hours and general (other products as well as PPE) stock usage decreased.
Improved housekeeping
– Product stock levels optimised due to real-time replenishment data
– Product range optimised, so only the product required for the job is made available to users in specific areas
– Large paper trails to keep track of stock issuance were eliminated due to online visibility.
Improved utilisation for the life of the product
– Real-time data identified users that were changing PPE product more than once a week
Elimination of excess usage (one, for now, one for later)
– Reports highlighted users that were taking more items than required for their job. By the end of month 1, excess usage had been eliminated.
Elimination of Users taking incorrect PPE
– Users were taking more expensive Kevlar gloves for jobs that required a different type of glove. Not only was this correct glove far more suitable protection for the job but was also less expensive.
Below is the return for this solution over 5 years based on the cost benefits demonstrated in year 1.
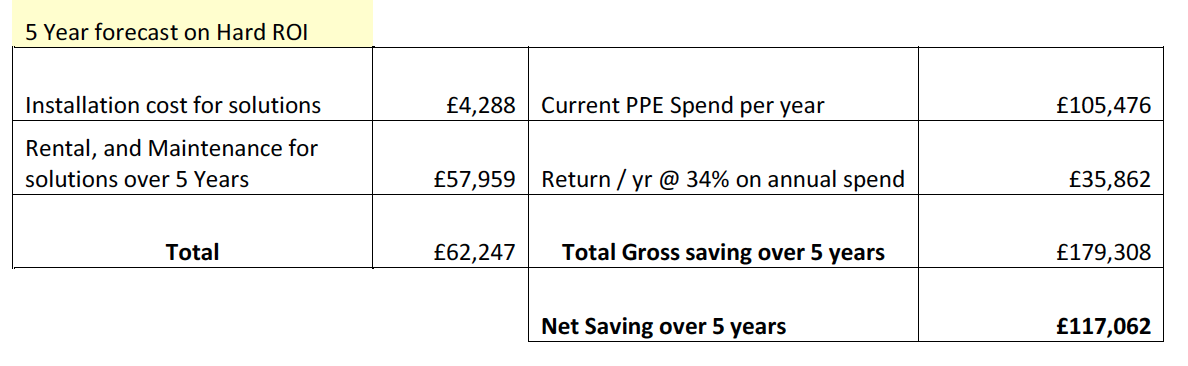
Soft Cost Savings
These savings are based on None Value Added activity through:
- Operator walk around time – Hourly labour cost
- Access time for MRO – Hourly labour cost
- Improved productivity – Production improvements in efficiency
- Improved efficiency & effectiveness in the purchasing process
- Defending litigation cases (for PPE) – Hourly labour cost
- Compensation payments – £50K typical settlement cost
- Savings in management data production, KPI’s etc.
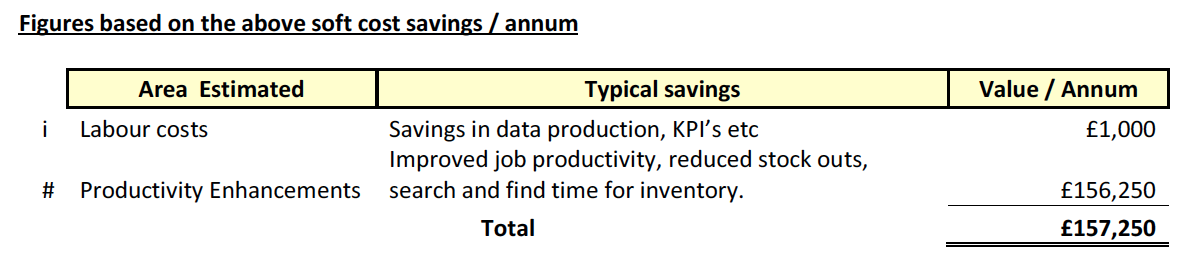
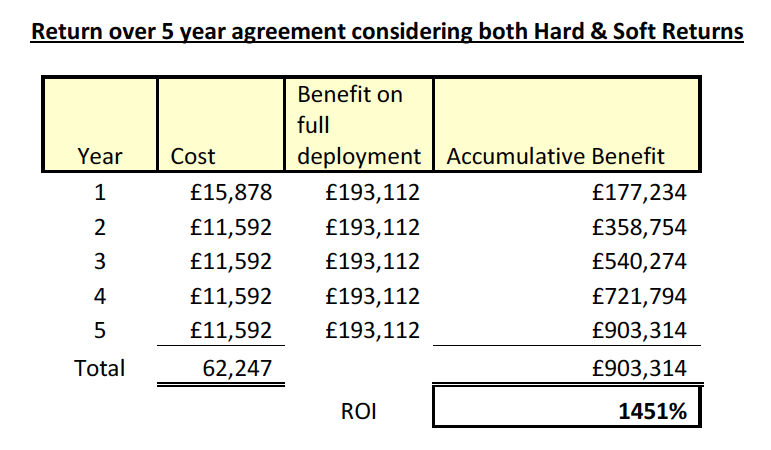